The Evolution of Distribution Arrester Technology
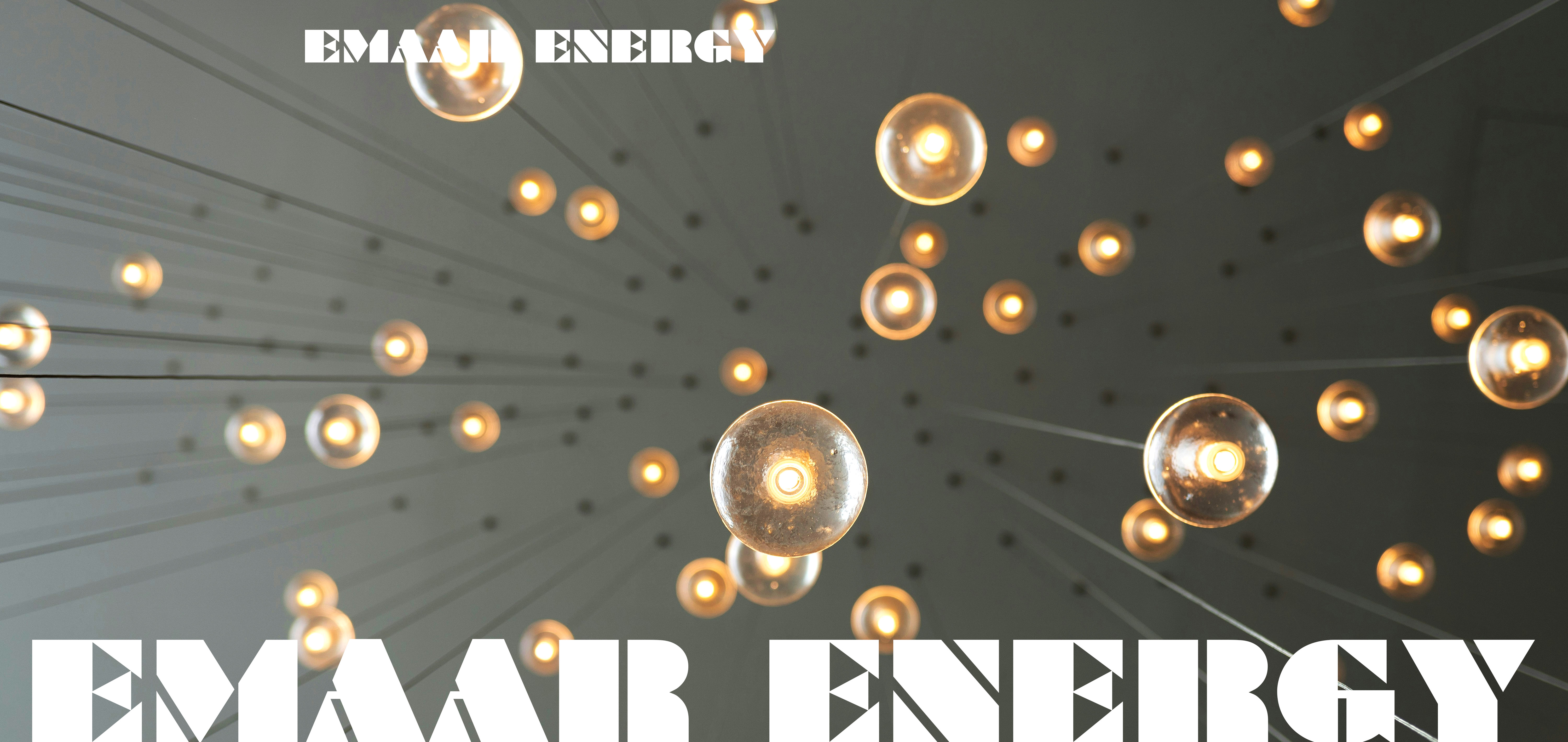
CHECK OUT THE LATEST IN
HYDRAULIC AND MECHANICAL TOOLS
Solar Solutions
Inverters & Storage
Solar microinverters play a crucial role in making solar energy more efficient, reliable, and accessible, thereby indirectly benefiting our lives in several ways:
1. Increased Energy Harvest (More Electricity):
Individual Panel Optimization: Unlike traditional string inverters where the entire array's performance is limited by the weakest panel (e.g., due to shade, dirt, or different panel orientations), microinverters are attached to each individual solar panel. This means each panel operates at its maximum power point independently.
Mitigation of Shading and Dirt: If one panel is shaded or dirty, only that panel's output is affected, not the entire string. This significantly increases the overall energy production of the solar system, leading to more electricity generated and greater savings.
2. Enhanced Reliability and Durability:
No Single Point of Failure: With a string inverter, if the inverter fails, the entire solar system stops producing power. With microinverters, if one microinverter fails, only that specific panel's output is lost, while the rest of the system continues to operate. This distributed architecture leads to greater system uptime.
Longer Lifespan: Microinverters generally have a longer lifespan (often 20-25 years) compared to string inverters (typically 10-15 years), aligning better with the lifespan of solar panels.
3. Improved Safety:
Lower DC Voltage: Microinverters convert DC (direct current) from the panels into AC (alternating current) right at the panel level. This eliminates the need for high-voltage DC wiring running across the roof and through the building, significantly reducing the risk of DC arc faults, which can be a fire hazard. This is a major safety advantage for homeowners, installers, and emergency responders.
4. Easier Monitoring and Diagnostics:
Panel-Level Monitoring: Microinverter systems allow for granular, panel-level monitoring of performance. This means you can see how much power each individual panel is producing.
Faster Troubleshooting: If a panel is underperforming, it's easy to pinpoint the exact panel and diagnose the issue (e.g., dirt, shade, or a faulty panel/microinverter), making maintenance and troubleshooting much simpler and quicker.
5. Greater Flexibility and Scalability:
Modular Design: Microinverter systems are highly modular. You can start with a smaller system and easily expand it by adding more panels and microinverters later, as your energy needs or budget allow.
Complex Roof Layouts: They are ideal for roofs with complex shapes, multiple orientations, or partial shading, as each panel can be placed optimally regardless of its neighbors. In essence, solar microinverters contribute to a more efficient, safer, reliable, and user-friendly solar energy experience, which directly translates to more affordable and consistent renewable energy for homes and businesses. This, in turn, supports reduced reliance on fossil fuels, lowers carbon emissions, and contributes to a more sustainable future.
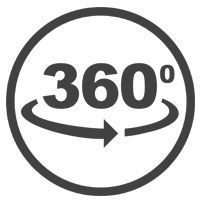
Omnidirectional Control
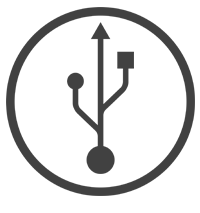
Smart connection
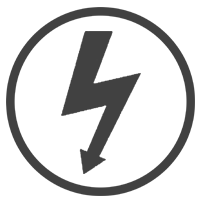
Anti Overvoltage
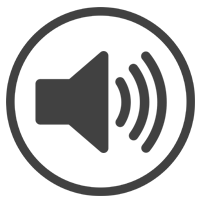
Early Warning
Electrical Panel
Panel customization
1. Enclosure Design & Specifications:
Dimensions and Form Factor: Panels can be custom-sized to fit available space, whether it's a tight closet, a large industrial plant room, or outdoor installation. This includes wall-mounted, floor-standing, free-standing, or modular designs.
Material: Options like galvanized steel, stainless steel, aluminum, or even specialized composite materials for specific environments (e.g., highly corrosive areas).
Environmental Protection (IP/NEMA Ratings): Customization to achieve specific Ingress Protection (IP) or NEMA ratings, indicating protection against dust, water, and other environmental factors (e.g., IP65 for outdoor use, NEMA 4X for corrosive environments).
Cooling/Ventilation: Integration of fans, vents, air conditioners, or heat exchangers for optimal temperature control within the enclosure, especially for panels housing sensitive electronics or operating in hot climates (like Vietnam).
Security: Custom locks, keying, or access control features.
Mounting Options: Specific mounting brackets, plinths, or frames.
2. Internal Component Selection & Layout:
Circuit Breaker Sizing and Type: Selecting the exact number, type (MCCB, ACB, MCB, etc.), and rating (amperage, breaking capacity) of circuit breakers to match the load requirements and fault levels of the installation.
Protection Devices: Integration of specific relays (overcurrent, earth fault, differential), surge protective devices (SPDs), residual current devices (RCDs), and other protective components.
Control Devices: Inclusion of contactors, motor starters (DOL, Star-Delta, soft starters, VFDs), programmable logic controllers (PLCs), timers, relays, and other automation components specific to the system being controlled (e.g., HVAC, pumps, machinery).
Metering and Monitoring: Integration of specific meters (voltmeters, ammeters, power factor meters, energy meters), current transformers (CTs), potential transformers (PTs), and smart monitoring devices for data acquisition and analysis.
Busbar Design: Custom sizing, material (copper/aluminum), and arrangement of busbars to handle required current levels and ensure proper segregation (e.g., Form 2, 3, 4 segregation for enhanced safety and maintainability).
Wiring and Cabling: Specific types of wiring, cable entries, terminal blocks, and labeling systems to meet local codes, safety standards, and ease of maintenance.
3. Functional & Operational Customization:
System Type: Designing panels for specific applications such as:
. Main Distribution Boards (MDB)
. Sub-Distribution Boards (SDB)
. Motor Control Centers (MCC)
. Automatic Transfer Switches (ATS) panels for generators
. Power Factor Correction (PFC) panels
. Building Management System (BMS) integration panels
. Control panels for specific industrial machinery or processes
Automation and Control Logic: Programming of PLCs, human-machine interfaces (HMIs), and other intelligent devices to implement custom control sequences, interlocks, alarms, and remote monitoring/control capabilities (e.g., smart home integration, industrial automation).
User Interface: Customizing the front panel with specific indicators (lights), push buttons, switches, and HMI screens for operator interaction.
Safety Features: Incorporating specific safety interlocks, emergency stop buttons, bypass switches, or arc flash mitigation features.
4. Compliance and Certification:
Standards Adherence: Ensuring the panel is designed and built to comply with relevant international (IEC, UL,NEMA) and local standards and regulations (e.g., Vietnamese electrical codes, safety regulations).
Testing and Documentation: Providing custom factory acceptance tests (FAT), site acceptance tests (SAT), and comprehensive documentation including wiring diagrams, component lists, and operating manuals.
Why is this important for the grid/end-users?
Optimal Performance: A customized panel precisely matches the electrical and control requirements, leading to more efficient and reliable operation of connected equipment.
Safety: Tailored designs ensure all safety standards are met for the specific environment and application,minimizing risks of electrical hazards.
Space Optimization: Custom dimensions allow for panels to fit into challenging spaces, which is often critical in urban environments or existing infrastructure.
Cost Efficiency: While customization has an upfront cost, it avoids over-specifying or under-specifying components, leading to long-term savings in energy consumption, maintenance, and avoiding costly retrofits.
System Integration: Custom panels seamlessly integrate with existing or new building management systems,automation platforms, and specific machinery.
Longevity and Durability: Materials and protection levels can be chosen to ensure the panel withstands the specific environmental conditions (humidity, temperature, dust) of its installation location, extending its lifespan.
Overhead and Underground Accessories
Key accessories for building our network
Overhead conductor accessories are absolutely essential components of a power network, playing a critical role in its safety, reliability, efficiency, and longevity. They are far from mere add-ons; they are integral to the very existence and stable operation of overhead power lines.
Here's why they are so important to the grid:
1. Structural Integrity and Support:
Holding the Line: Conductors are heavy and subject to forces like wind, ice, and their own tension. Accessories like suspension clamps, strain clamps, crossarms, and various brackets literally hold the conductors in place, transferring their weight and tension securely to the poles or towers. Without these, conductors would simply fall to the ground.
Maintaining Sag and Clearance: Proper tensioning and support, facilitated by accessories, ensure that conductors maintain safe sag levels. This prevents them from touching the ground, trees, buildings, or other lines, which would cause short circuits and outages.
2. Electrical Isolation (Insulation):
Preventing Short Circuits: Insulators are paramount. They physically and electrically separate the live conductors from the grounded poles/towers and other structures. This prevents electricity from flowing to unintended paths (ground faults), ensuring that power is delivered only where it's supposed to go.
Ensuring Safety: Proper insulation is vital for public and worker safety, preventing electrocution hazards.
3. Electrical Continuity and Connection:
Joining Conductors: Splice connectors are used to join different sections of conductor together, ensuring a continuous electrical path over long distances.
Tapping Off Power: Tap connectors (e.g., insulation piercing connectors, parallel groove clamps) allow for safe and reliable connections to branch lines, enabling power to be distributed to various consumers or other parts of the grid. These connections must be robust to carry current efficiently without overheating.
4. Protection of Conductors and Equipment:
Vibration Control: Vibration dampers (like Stockbridge dampers) are critical for mitigating aeolian vibration (wind-induced oscillations) that can cause fatigue damage to conductors and accessories, leading to failures over time.
Arc Protection: Some accessories, particularly for covered conductors, include arc protection devices to prevent damage from electrical arcs.
Wildlife Protection: As discussed, insulating covers and animal guards prevent outages and equipment damage caused by animals, while also protecting the wildlife itself.
Mechanical Protection: Armor rods protect conductors from abrasive wear and stress concentration at support points, extending their lifespan.
5. Flexibility and Maintainability:
Modular Design: Accessories enable a modular construction of the grid, making it easier to install, repair, and upgrade specific sections without needing to rebuild entire lines.
Load Management: Specific accessories allow for flexibility in rerouting power or isolating sections for maintenance or fault clearance, improving the grid's ability to respond to issues.
6. Efficiency and Performance:
Reduced Losses: Well-designed and properly installed accessories ensure low resistance connections, minimizing energy losses (I²R losses) along the line. Poor connections can lead to hot spots, increased losses, and potential failures.
Optimized Performance: By maintaining conductor integrity and stability, accessories contribute to the overall efficient transfer of electrical energy.
In essence, overhead conductor accessories are the unsung heroes of the power grid. They are the intricate pieces that bind the entire system together, ensuring that electricity generated at power plants can safely and reliably reach homes, businesses, and industries. Without them, the vast network of overhead lines that powers our modern world simply wouldn't function. Their importance directly translates to the reliability, safety, and economic viability of the entire electrical infrastructure.
Wildlife Protection Solutions
We have family. Wild animals have, too. In EMAAR, we want to protect them from electrical connections
Wildlife protection devices are crucial in power networks for a dual purpose: to protect wildlife and to protect the power network itself. The interaction between animals and electrical infrastructure can have severe consequences for both, leading to environmental harm and significant operational issues for utilities. Here's a breakdown of why we need them:
1. Protecting Wildlife
Preventing Electrocution: Many birds (especially large raptors like eagles, hawks, and owls), squirrels, snakes,and other climbing animals can be electrocuted when they come into contact with energized power lines or equipment. This often happens when they bridge the gap between two live conductors or between a live conductor and a grounded part of the pole or structure. Wildlife protection devices aim to prevent this by insulating or increasing the clearance around live parts.
Preventing Collisions: Large birds, particularly those that fly at night or in flocks, can collide with power lines that are difficult for them to see, especially in low light conditions or adverse weather. This results in injury or death for the birds.
Habitat Preservation: While power lines themselves can fragment habitats, mitigating direct harm to wildlife helps preserve populations, especially for endangered or protected species.
2. Protecting the Power Network
Preventing Power Outages: Wildlife contact is a significant cause of power outages globally. When an animal causes a short circuit or "flashover," it often triggers protective devices (like circuit breakers or reclosers) to trip,cutting off power to a potentially large area. These outages are inconvenient for consumers, can cause economic losses, and pose risks to critical services.
Minimizing Equipment Damage: The arcing and short circuits caused by wildlife contact can severely damage expensive electrical equipment such as transformers, insulators, and power lines. This leads to costly repairs and replacements for utility companies.
Reducing Fire Risk: In dry conditions, a wildlife-induced fault can generate sparks or arcs that ignite surrounding vegetation, leading to devastating wildfires. This is a particular concern in areas prone to drought or with high fuel loads.
Improving System Reliability: By reducing the frequency of wildlife-related faults, utilities can improve the overall reliability and stability of the power grid, ensuring more consistent power delivery to customers.
Avoiding Financial Penalties: Many regulatory bodies impose fines on utilities for outages, especially if they are preventable. Investing in wildlife protection devices can help utilities avoid these penalties.
Meeting Environmental Regulations and Corporate Social Responsibility: Utilities are increasingly held accountable for their environmental impact. Implementing wildlife protection measures demonstrates a commitment to biodiversity conservation and sustainable practices, which can improve public perception and meet regulatory requirements.
Pole-Top Switch
Protect our grid from potential risks
Pole top switches, also known as pole-mounted disconnect switches or load break switches, are essential components of electrical distribution networks for several critical reasons:
1. Circuit Isolation for Safety and Maintenance:
Safety for Personnel: This is arguably their most vital function. When maintenance, repairs, or upgrades are needed on a section of the power line or associated equipment (like transformers or reclosers), pole top switches are used to physically disconnect that section from the live electrical grid. This creates a visible,isolated break, ensuring the safety of workers who are performing tasks on the de-energized line.
Equipment Protection: By isolating a faulty section, these switches prevent further damage to equipment and prevent the fault from spreading to other parts of the grid.
2. Sectionalizing the Grid:
Minimizing Outages: Electrical grids are divided into sections. If a fault (like a short circuit from a fallen tree branch or equipment failure) occurs in one section, pole top switches can be opened to isolate only that faulty segment. This prevents a complete blackout of the entire feeder or circuit, allowing power to be restored quickly to unaffected areas. This is known as "sectionalizing" and greatly improves system reliability and reduces the impact of outages on consumers.
Bypassing Equipment: Some pole top switches are specifically designed as "bypass switches" to allow maintenance on critical equipment (like reclosers or voltage regulators) without interrupting power to the downstream consumers.
3. Load Breaking Capability (for Load Break Switches):
While simple disconnect switches are operated when there's no current flowing, load break switches are a type of pole top switch designed to safely interrupt or "break" normal load currents. This allows utility personnel to switch circuits on or off under load conditions, providing flexibility in power flow management.
4. Flexibility in Power System Operation:
Rerouting Power: In an emergency or during planned network reconfigurations, pole top switches allow operators to reroute power from alternative sources to maintain supply to consumers. This can be critical for maintaining service during peak demand or in the event of upstream equipment failures.
Network Optimization: They facilitate the optimization of power flow to balance loads, reduce losses, and improve voltage profiles across the distribution network.
5. Integration with Smart Grid Automation (for Automated Switches):
Modern pole top switches can be equipped with remote control and monitoring capabilities. These "distribution automation switches" are crucial for Smart Grid initiatives, allowing utilities to:
. Remotely operate switches, reducing response times to outages.
. Monitor real-time line conditions (voltage, current, power quality).
. Automatically detect and isolate faults, significantly reducing outage durations.
. Optimize power flow and manage demand more efficiently.
Transmission Line Accessories
Transmission line accessories are indispensable to the functioning, safety, and reliability of the entire power grid
1. Mechanical Support and Stability:
Holding Conductors: Accessories like suspension clamps and tension/dead-end clamps are designed to securely attach the heavy transmission line conductors to the insulators and, ultimately, to the towers. Without them, the conductors would simply fall.
Managing Tension: Transmission lines are under immense mechanical tension. Tension clamps are engineered to withstand and transfer these forces to the towers, preventing the conductors from pulling loose.
Maintaining Clearances and Sag: Accessories help establish and maintain the precise sag (the dip) in the conductors, ensuring they stay at a safe distance from the ground, buildings, and other lines, preventing dangerous contact and short circuits.
Structural Integrity: Various link fittings, clevises, shackles, and bracing hardware connect different components of the tower and insulator strings, ensuring the entire structure is robust and stable against environmental forces like wind, ice, and seismic activity.
2. Electrical Performance and Efficiency:
Vibration Control: Vibration dampers (e.g., Stockbridge dampers) are crucial for long transmission spans. Wind can cause conductors to vibrate (aeolian vibration), leading to fatigue damage and eventual strand breakage. Dampers absorb this energy, preventing costly conductor failures and maintaining line integrity.
Sub-Conductor Spacing: For bundled conductors (multiple conductors per phase), spacers and spacer-dampers maintain the correct distance between individual conductors within the bundle. This prevents them from clashing together due to wind or short-circuit forces, which would cause flashovers and outages. They also help in uniform current distribution and reduce corona losses.
Corona and Arcing Control: Accessories like corona rings (grading rings) and arcing horns are vital for high-voltage lines. Corona rings help to distribute the electric field evenly around the insulator strings and connections, reducing partial discharges (corona) that cause energy loss, radio interference, and degradation of insulation. Arcing horns provide a preferential path for lightning or switching surges to flash over, protecting the expensive insulators and conductors from direct damage.
Low Resistance Connections: Splice and repair sleeves, as well as various connectors, ensure robust, low-resistance electrical connections between conductor sections or for tapping off power. Poor connections can lead to hot spots, increased energy losses, and eventual failure, causing outages.
3. Safety and Protection:
Lightning Protection: Ground wires (or shield wires), supported by specific accessories, run along the top of transmission towers. These wires intercept lightning strikes, diverting the massive current safely to the ground through the tower structure, protecting the phase conductors from direct hits and subsequent outages.
Insulator Protection: As mentioned, arcing horns protect insulators from being damaged by flashovers during overvoltage events.
Wildlife Protection: While more common on distribution, some transmission lines in sensitive areas might use bird flight diverters or other deterrents to prevent collisions or electrocutions of large birds, which can cause both bird fatalities and line outages.
Personnel Safety: Properly installed and maintained accessories ensure the structural integrity of the line, which is crucial for the safety of maintenance personnel working on or near energized lines.
4. Operational Flexibility and Maintenance:
Sectionalizing: While not an "accessory" in the same way, the points where lines are joined or terminated (often using accessories) facilitate the ability to isolate sections of the line for maintenance or in the event of a fault.
Monitoring Integration: Some modern accessories can integrate sensors for real-time monitoring of line conditions (e.g., temperature, sag, vibration), contributing to smart grid initiatives and predictive maintenance.
In summary, transmission line accessories are not just add-ons; they are highly engineered components that collectively enable the safe, reliable, and efficient transmission of electrical power across vast distances. They ensure the physical integrity of the lines, optimize electrical performance, protect against environmental and electrical stresses, and facilitate maintenance, all of which are absolutely critical for a stable and functioning power grid.
Safety tools
Any device, equipment designed to protect individuals from accidents
Safety tools are incredibly important for a multitude of reasons, spanning personal well-being, legal compliance, and business efficiency. Here's a breakdown of why they are so crucial:
1. Protecting Lives and Preventing Injuries:
- Primary Purpose: This is the most fundamental reason. Safety tools (often referred to as Personal Protective Equipment or PPE) act as a barrier between workers and potential hazards. This includes items like hard hats, safety glasses, gloves, respirators, safety shoes, ear protection, and fall arrest harnesses.
Reducing Severity: Even if an accident does occur, appropriate safety tools can significantly reduce the severity of injuries, turning a potentially fatal incident into a minor one.
Saving Lives: In high-risk environments, safety tools can literally be the difference between life and death.
2. Ensuring Legal Compliance and Avoiding Penalties:
Employer Responsibility: In most countries, employers have a legal and moral obligation to provide a safe working environment for their employees. This often includes providing and enforcing the use of appropriate safety tools.
Regulatory Standards: Government bodies (like OSHA in the US or similar organizations in other countries) set strict safety regulations and standards that workplaces must adhere to. Failure to comply can result in hefty fines, legal action, and even imprisonment for responsible parties.
Reducing Liability: By providing and ensuring the proper use of safety tools, companies can significantly reduce their liability in case of workplace accidents.
3. Boosting Productivity and Efficiency:
Worker Confidence: When employees feel safe and protected, they are more confident in performing their tasks.This reduces anxiety and allows them to focus on their work, leading to increased productivity.
Reduced Downtime: Accidents lead to downtime for investigations, first aid, medical attention, and repairs. By preventing accidents, safety tools contribute to continuous operations and higher overall efficiency.
Lower Absenteeism: Fewer injuries and illnesses mean fewer sick days and less absenteeism, keeping the workforce robust and consistent.
4. Reducing Costs:
Direct Costs: Accidents incur significant direct costs, including medical expenses, workers' compensation claims, repair or replacement of damaged equipment, and increased insurance premiums.
Indirect Costs: There are also indirect costs like lost productivity, administrative costs for accident investigation, legal fees, damage to company reputation, and employee turnover. Investing in safety tools is often far more cost-effective than dealing with the aftermath of an accident.
Equipment Longevity: Sometimes, safety tools also protect the equipment itself, preventing damage and reducing repair or replacement costs.
5. Improving Employee Morale and Company Culture:
Demonstrating Care: Providing proper safety tools shows employees that their well-being is a priority for the company. This fosters a sense of trust and appreciation.
Positive Work Environment: A safe workplace contributes to a positive and healthy work environment, which can lead to higher job satisfaction, increased loyalty, and reduced employee turnover.
Safety Awareness: A strong emphasis on safety tools promotes a culture of safety awareness throughout the organization, encouraging everyone to be vigilant and responsible.